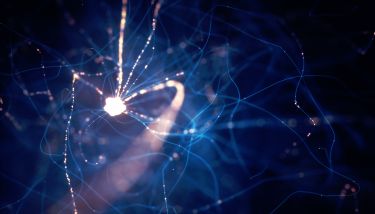
Health & Medicine
Reading the body’s electrical signals to treat illness
A new material designed to harvest up to 400 times more energy from movement than currently possible has potential applications in biomedicine and geospatial monitoring
Published 27 January 2023
Since the ancient Greeks, humankind has known that if you bring two things into contact, a small amount of electricity is created. One example is that we can rub a balloon with our hair and generate enough electricity to stick it to the ceiling.
The same principle has been applied to our new research published in the journal Small, which discovered how to manufacture optimal energy generation between very minute fibre layers in material.
Each of these tiny fibres is around 100 times thinner than a human hair. They are composed of polymers that are repeating chains of the same units. In this case, we used the polymers ethylene-vinyl acetate – which among other uses gives running shoes their ‘springiness’ – and polylactic acid – which happens to come from the same acid that causes muscle cramps after exercise.
We alternated the two different types of fibres into layers in a very specific way, to make ‘laminates’. These laminates are made of many stacked microscopic layers, and each laminate patch is composed of tens of thousands of fibres.
Health & Medicine
Reading the body’s electrical signals to treat illness
Wherever there is any movement around the layers of the fibres, electricity is generated from the friction between each layer.
We altered the size and texture of these fibre layers and ordered them in very specific ways to optimise the friction and contact electrification, and ultimately generate the maximum charge.
Our research demonstrated that by using this ordering, we can make around 400 times more electricity from motion than was previously possible from these materials. Since we can always introduce more interfaces by using thinner fibres, this type of energy generation is very scalable.
This has exciting potential applications where there is a lot of movement, but now it’s only on a very small scale - for example, using human motion to power a smartwatch or recharging an implantable device such as a pacemaker.
In the biomedical field, there is the potential to catch the energy from blood flowing through an artery or vein to keep an insulin pump going for longer for example.
This capability is also very powerful in the sensing area, particularly, if there is a need to measure very small vibrations from the environment, like monitoring minor seismic activity or changes in water flow, or to power sensors in remote locations where you don’t get a lot of sun.
Sciences & Technology
The nanowires building greener nanodevices
In these scenarios, you can’t use solar cells or easily replace a battery. Being able to harvest energy just from the vibrations in the ground to keep the internet and other critical infrastructure working has significant potential.
The research was done in collaboration with Professor Andris Sutka at Riga Technical University in Latvia using a process called electrospinning to create the polymer fibres. By adjusting the electrospinning tool, we were able to adjust what polymer we were spinning out, and its thickness.
One of the challenges with the research was ordering and controlling how the polymer layers interact with each other. It’s very tricky to control how each fibre vibrates in relation to the other and if you get the ordering wrong, the electricity generated cancels out.
Another challenge is that the polymers are very soft and can deform easily. So, when we try to look inside the materials to assess structure, they can melt or break. This makes characterising the materials difficult and the process of creating these microscopically small polymer laminates is very slow.
Despite these challenges, we have come a very long way since the ancient Greeks’ first understanding of electrical charge.
Our research over the past three years has looked at plastics and how to control chemistry to influence the charge. It is the culmination of new understandings of how plastics charge, enabled by quantum physics in the 1900s and the development of instrumentation that lets us accurately detect what’s going on – as we need to measure very small currents at very precise time intervals.
Health & Medicine
Translating thought into action
We’re now looking at different ways we can use the energy we generate. This study produced 400 times more energy than ever before. However, it’s still a relatively small amount, so the applications will be different to say a solar cell or other types of mass-energy generation.
At the moment we’ve only looked at two types of plastics, but there are hundreds more out there that will let us generate even more energy.
It’s more likely that the energy generated will be used at its source, so there is no loss of this small but precious energy in the transfer process. There are also potential applications in acoustic energy harvesting – where you harvest the energy from people talking and vibrations.
Now that we know we can use these fibres and order them to make a charge, we can do different form factors such as a hollow lining for inside a pipe, or padding that can record how much vibration a shipped package goes through, and start to engineer it to solve different problems. This may have applications if we look at coating pipes or building pylons to harness infrastructure energy, for example.
The transformative potential of this discovery is exciting, albeit some years away as we learn more about how to harness the energy from small movements to power big advances.
This work was completed with the assistance of the Melbourne Centre for Nanofabrication, Artis Linarts, Institute of Technical Physics, Faculty of Materials Science and Applied Chemistry, Riga Technical University, and Andris Šutka, Institute of Materials and Surface Engineering, Faculty of Materials Science and Applied Chemistry, Riga Technical University.
Banner: Getty Images