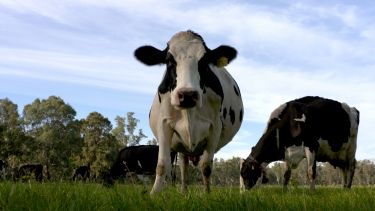
Environment
Are these Australia’s happiest dairy cows?
Kenny Oluboyede’s serendipitous journey from rural Nigeria to the University of Melbourne’s robotic research dairy in Dookie has made him the University’s own cow whisperer
Published 10 July 2017
When I came down to Dookie for the job interview I took one look at the dairy and fell in love with the whole idea. I said to the University, even if you don’t give me this job I’m going to come down here anyway to keep visiting this place. It was brilliant to see the cows milking themselves voluntarily. The robotic dairy is completely different from a conventional dairy.
The first thing you notice is the quiet. There are no dogs rounding up the cows, there is no chasing or yelling at the cows. When I walk around them, they don’t feel like I am harassing them, so they feel a lot more comfortable around people. In a conventional dairy you have to move the cows in to be milked at a set time when someone is there to do it. But here we don’t have to do that because the cows wander in voluntarily to be milked. And cows are surprisingly very polite. They are happy to wait for the cow in front to have its turn and go through the dairy. It makes a big difference to their welfare, their health and their wellbeing.
Just like us, cows don’t want to do everything at the same time. Not all of us like to get out of bed at 5am. Some of us want to lie in bed until 7am. It is the same with cows and when they want to be milked. Keeping the cows comfortable and unstressed is one of the big plusses in a setting like this. The dairy even has a backscratcher that the cows can rub against after they’ve been milked. And the result is more and better milk production. We’ve won Dairy Australia’s milk quality awards two years in a row, putting us among the top 100 farms with the best milk quality out of over 6500 dairy farms in Australia.
Environment
Are these Australia’s happiest dairy cows?
Once the cow enters the dairy to be milked we collect all sorts of data from in-built sensors. There is data on their body weight, the individual milk quality, the milk temperature and colouration of the milk, and the cow’s own activity. We can then compare that data with our own observations of how the cows are behaving and that way you learn a lot.
You know the cows are happy when you see them relaxed and quiet, and you want to see over half of them ruminating, or chewing their cud. This is when the cow re-chews regurgitated fodder as part of their digestion process and it is a very important indication of their wellness. When they are chewing their cud you know they have the right fibre content in their diet. And we can keep track of how many times each cow chews its cud. All the cows here wear an RFID (radio-frequency identification) transponder that has a small microphone. It is strapped to the left flank of their necks, and it allows us to listen to how frequently they are chewing their cud. Ideally, we like to see a rumination of roughly 400 minutes per cow per day. All that data is recorded on the computers so we can monitor it.
Sciences & Technology
Silage: Rocket-fuel for cows
I joke that I’m a cow whisperer. But it is really about spending the time observing the cows and tracking the data we collect. The cows are the best judges of what they need. If it is right they will tell you, and if it is wrong they will tell you by their behaviour.
For instance, it was by just observing their behaviour that the cows told me we had to change the gate opening time.
When cows come in from grazing in one part of the farm, they can only have access to their next grazing after they have gone through the dairy for milking. The dairy is the control station that lets the cows transit through each pasture block at the set time. The farm is divided into three blocks A, B and C, with cows getting fresh pasture in each block three times a day. We give them enough feed for about an eight-hour period after each visit. After roughly that time, they will be coming to the dairy voluntarily to transit to the next block for grazing. This way, we are able to manage our cows as well as our pasture.
But when I first started here I noticed that a lot of the cows were starting to line up at the gates for milking in the evening as early as 5pm when the gates weren’t set to open until 7pm. After observing the cows waiting in the laneway when they were not due for their next grazing, I decided to bring forward the gate opening time, and it made an instant difference. Production went up because they weren’t waiting at the gate, getting stressed and not eating. So I let the cows determine when they like to move from one part of the farm to another for grazing, and basically, just move the gate times to soothe them, and it works!
The technology not only monitors the cows, it also tells me when things aren’t working, even when I’m in bed asleep. The system is set up with computer generated calls to alert me, or the other staff, if there is something not right with the machine; for example cows failing milking, a filter needing replacing, or detergent supply is low. I’ve had calls at every time of the day and night you can think of, particularly during the early days after the installation. One time I ended up just sleeping in the dairy because the alarm kept going off when it took longer than expected to fix the problems. But if you are doing everything by the book you will get less late night alarms. These days it might happen about two or three times a month.
I studied to become an engineer, not a farmer, but a lot of things in my life haven’t been planned. I grew up in Nigeria, and most of my early childhood was spent in a country town about twice the size of Dookie. In that community, farming is the number one trade, and I spent a lot of time on my parent’s farm. In my teenage years, we moved to the city and after graduating from university, my brothers and I started a small multimedia business, which I managed, but it became boring for me. Then I saw an opportunity for a foreign exchange program in Australia and thought, “why not?” Suddenly I found myself in Western Australia on the Margaret River working on a dairy farm. It was hard work, but the animals were intriguing. They are such big and heavy creatures. Of course I don’t see them as big any more, I see them as little pets, but at first they seemed really big. And from the start I was fascinated with how cows are managed and how you encourage them to do what you want them to do.
Environment
Dairy’s (climate) changing future
After 6 months in WA, I went travelling around Australia and fell in love with the country. I returned back home after a year and I realised I wanted to come back to Australia, but it wasn’t easy. I ended up going to the UK but it wasn’t for me. Finally, there was a work opportunity to come to New Zealand because of my dairy farming experience. So there I was, back on a dairy farm as an assistant herd manager in New Zealand.
Those early mornings getting up in sub-zero temperatures weren’t at all nice for an African boy! But I decided to give dairy farming a go and so I went through all the industry training programs on offer in New Zealand up to a diploma. It was while I was studying that I got a job working on Lincoln University’s commercial dairy farm in Christchurch. After about two-and-half years, I finally got the opportunity to come back to Australia and work at the University of Queensland’s research dairy at Gatton, west of Brisbane. It was really exciting work and while I was there I also completed a master’s degree in agri-business. Then about three years ago the opportunity came up to work here at the Dookie robotic dairy.
So almost by co-incidence I’ve spent the last nine years working at university dairy farms. I have really enjoyed being at the forefront of research and development. It is a privilege to be working in a place with industry best practices, and with people who are early adopters of new technologies. It is one of the things that attracts me to sticking around universities.
As told to Andrew Trounson, University of Melbourne.
Banner Image: Paul Burston / University of Melbourne