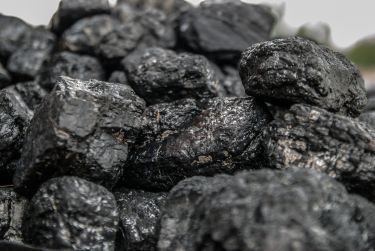
Politics & Society
Coalface tactics
Mapping the massive network of tunnels that give miners underground access to mineral ores is an expensive and time-consuming process, but new optimisation software, inspired by the complexity of the microchip, could save the industry millions
Published 11 October 2017
The wires of a tiny microchip may seem a world away from a huge underground mine full of complex tunnels, but for a team of University of Melbourne researchers, the design principles are very similar.
More than 20 years ago, Professor Doreen Thomas and Professor Hyam Rubinstein were working on innovative methods of network optimisation - which aims to ensure optimal usage for system resources, as well as improving productivity and efficiency - in the design of microchips.
“When designing microchips, you have wiring that needs to link up multiple nodes on the chip,” says Professor Thomas.
“There are thousands of nodes that need to connect together and you want the wiring to be as short as possible so that you have the least number of faults, allowing the electronics to be as fast as possible.”
Professor Thomas and Professor Rubinstein, who set up software company MineOptima, applied their work in network optimisation to the design and planning of complicated, underground tunnel networks.
And their innovation is getting attention. Recently, international mining software and consulting firm RPM Global, acquired MineOptima.
The software is used to design the most efficient network for underground mine access tunnels; these are large, complicated networks that can run up to 30 kilometres underground.
“It is much more difficult than dealing with microchips, as we are working in a three-dimensional space,” says Professor Thomas.
“The problem is you have an entry and exit point for the mine on the surface, and a number of underground locations on ore bodies that the miners need to reach. They then have to drive huge haulage trucks and other pieces of equipment down there to access the ore and haul it back to the surface through the network.”
The MineOptima software relies on detailed geological information obtained from exploratory drilling that maps out the locations of ore bodies and other underground features such as faults and weak ground. The software then uses algorithms developed by the University of Melbourne Network Research Group to explore a range of possibilities for safe and optimal access tunnels, plotting their possible location.
The research group includes Associate Professor Marcus Brazil, Senior Research Fellow Peter Grossman, Laureate Professor Nick Wormald from Monash University and Emeritus Professor David Lee with the University of South Australia.
Professor Thomas says that there are complex rules that underground tunnels need to satisfy, such as precise constraints on the gradients of the incline and the decline.
“The gradient constraint is significant because the huge haulage trucks can only drive up a very shallow gradient. Networks need to slope very gently from the ore bodies to the surface. The other constraint is that the large trucks can only turn along wide corners in a tunnel.”
The software takes these restrictions into consideration – plotting the shortest network of paths between the mine’s entrance and the various points around the underground orebody.
“The mine planner has the orebody in front of them in three dimensions, and then they can choose a range of locations from which they want to access the ore zone,” Professor Rubinstein says.
He says that as surface ore deposits are gradually used up, miners need to access ore bodies further and further underground.
“A big challenge for mining going forward is that they are going to have to go deeper. So, we need to help answer the challenge, how do you mine safely and economically at depth?”
“Deeper mining will require more automation for safety and to cope with higher temperatures and ventilation requirements. Our access network optimisation research and software gives mining companies important tools to tackle these challenging tasks.”
Professor Thomas says that open cut mines require all the surface earth and rocks to be removed from the site, either going to waste or going to the mill for processing.
Politics & Society
Coalface tactics
“In an underground mine, you want to leave as much dirt or rock down there and map out these tunnels in an optimal way, in order to minimise the costs of development and haulage.”
Professor Rubinstein says that at the moment, in order to design a mine, mine planners need to conduct a number of feasibility studies, after which they might only come up with one or two designs.
“The idea with our software is that it allows you to create 200 access network designs in two weeks instead of two designs in six months.”
Professor Thomas says that whether or not an underground access tunnel network is mapped out optimally might determine whether or not a mine can go ahead.
“Access networks are a huge financial burden on a mine.
“If our software can save a few percent of the length of the tunnels, it can save millions of dollars over the life of the mine.”
Banner image: GettyImages